
In fact, numerous piezoelectric applications produce quasi-static measurements, and other applications work in temperatures higher than 500 ☌. However, it is not true that piezoelectric sensors can only be used for very fast processes or at ambient conditions. While quartz sensors must be cooled during measurements at temperatures above 300 ☌, special types of crystals like GaPO4 gallium phosphate show no twin formation up to the melting point of the material itself. The main effect on the piezoelectric effect is that with increasing pressure loads and temperature, the sensitivity reduces due to twin formation.
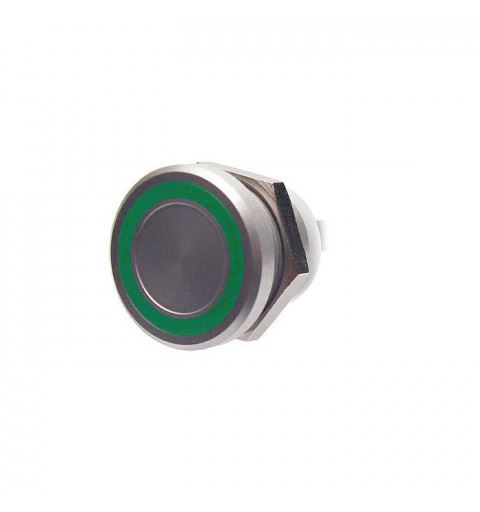
Elevated temperatures cause an additional drop in internal resistance and sensitivity. In conventional readout electronics, imperfect insulating materials and reduction in internal sensor resistance causes a constant loss of electrons and yields a decreasing signal. A static force results in a fixed amount of charge on the piezoelectric material. One disadvantage of piezoelectric sensors is that they cannot be used for truly static measurements.
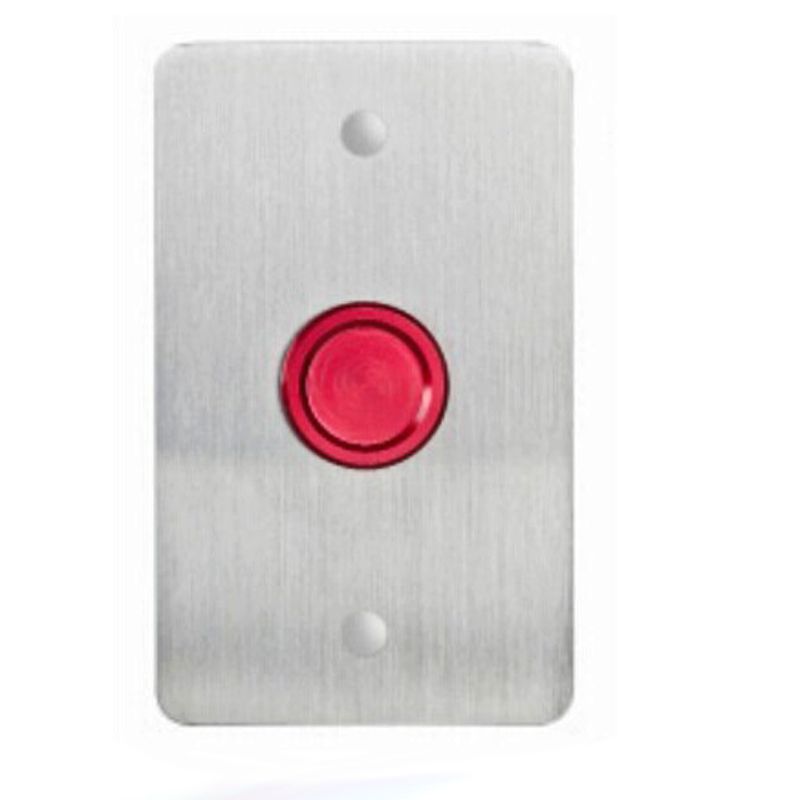
Gautschi in Piezoelectric Sensorics (2002) offers this comparison table of characteristics of piezo sensor materials vs other types: This effect is also common to piezoceramic materials. Tourmaline shows pyroelectricity in addition to the piezoelectric effect this is the ability to generate an electrical signal when the temperature of the crystal changes. Some materials used (especially gallium phosphate or tourmaline) are extremely stable at high temperatures, enabling sensors to have a working range of up to 1000 ☌. Additionally, piezoelectric technology is insensitive to electromagnetic fields and radiation, enabling measurements under harsh conditions. This gives piezoelectric sensors ruggedness, an extremely high natural frequency and an excellent linearity over a wide amplitude range. Even though piezoelectric sensors are electromechanical systems that react to compression, the sensing elements show almost zero deflection. The high modulus of elasticity of many piezoelectric materials is comparable to that of many metals and goes up to 10 6 N/m². The rise of piezoelectric technology is directly related to a set of inherent advantages. The sensors are either directly mounted into additional holes into the cylinder head or the spark/glow plug is equipped with a built-in miniature piezoelectric sensor. In the automotive industry, piezoelectric elements are used to monitor combustion when developing internal combustion engines. They have been successfully used in various applications, such as in medical, aerospace, nuclear instrumentation, and as a tilt sensor in consumer electronics or a pressure sensor in the touch pads of mobile phones. Since then, this measuring principle has been increasingly used, and has become a mature technology with excellent inherent reliability. Pierre Curie discovered the piezoelectric effect in 1880, but only in the 1950s did manufacturers begin to use the piezoelectric effect in industrial sensing applications. They are used for quality assurance, process control, and for research and development in many industries. Piezoelectric sensors are versatile tools for the measurement of various processes.
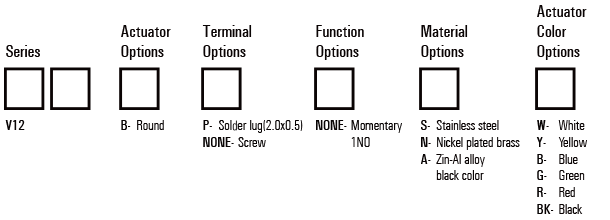
The prefix piezo- is Greek for 'press' or 'squeeze'. Type of sensor A piezoelectric disk generates a voltage when deformed (change in shape is greatly exaggerated)Ī piezoelectric sensor is a device that uses the piezoelectric effect to measure changes in pressure, acceleration, temperature, strain, or force by converting them to an electrical charge.
